Cool Cut: Laser and water for precise ceramic processing
Pulsar Photonics RDX1000 LWJ: Brittle-hard materials under control with the laser-water process
With the RDX1000 LWJ, Pulsar Photonics is launching a new generation of systems for precision machining. The combination of classic laser processing and laser waterjet technology from Synova enables high-precision cuts in ceramics, silicon carbide and hard metals – without thermal damage or mechanical wear.
“As part of the Schunk Group, we are pursuing the goal of further developing innovative manufacturing technologies for brittle-hard materials,” explains Dr. Stephan Eifel, Managing Director of Pulsar Photonics GmbH, Aachen. “With the RDX1000 LWJ, we are now enabling processing that was previously only possible with elaborate mechanical processes or complex post-processing steps.”
The RDX1000 LWJ is based on Synova’s patented Laser MicroJet process, which guides a laser beam over several millimetres in a fine water jet. As a result, the beam guidance remains stable while the material is cooled at the same time. “This combination gives us processing depths and precision that would not be achievable with conventional laser processes,” summarizes Eifel.
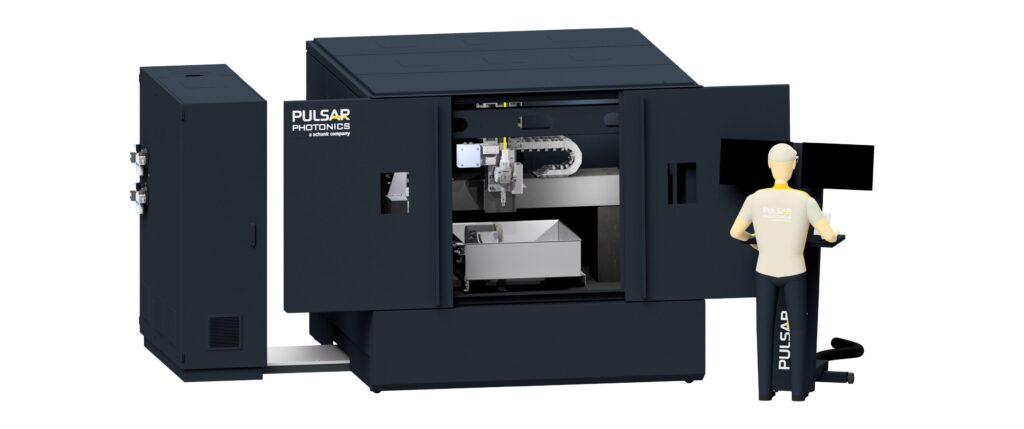
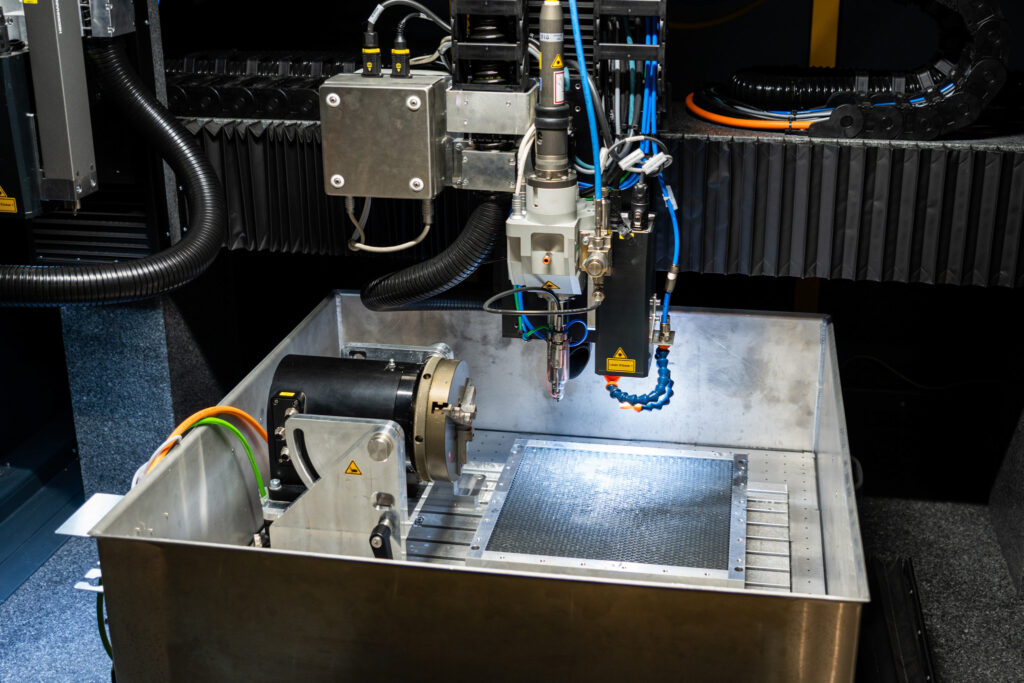
Deep cuts in thick materials
In addition, typical laser ablation processes for cutting often only achieve an aspect ratio of 1:3 to 1:5. This means that a kerf one hundred micrometers wide only reaches up to 500 micrometers deep into the material. Wider kerfs must be selected for deeper cuts, which leads to longer process times. With the RDX1000 LWJ, however, aspect ratios of up to 1:100 can be achieved – a dimension that was previously only possible with complex mechanical processes. “For example, we can drill or cut a structure just 100 micrometres wide into a 10 millimetre thick ceramic – this opens up completely new possibilities in production,” emphasizes the expert.
Another unique selling point is the combination of two processing stations: In addition to water-guided laser processing, a separate dry processing station is also available. “This gives our customers maximum flexibility,” says Dr. Eifel. “They can use both classic laser processes and the laser waterjet for particularly demanding machining tasks.”
This versatility makes it possible to implement hybrid processing strategies. For example, materials can first be structured and then precisely drilled through with the laser waterjet – an advantage in the production of complex functional components.
Testing in the Schunk MACHLab
The MACHLab, the Schunk’s group-wide application center, tests the technology under real production conditions. “Here we create a development environment in which new applications can be transferred directly to production,” emphasizes Dr. Eifel. Schunk sees great potential in the processing of 3D-printed silicon carbide in particular, as well as in the production of high-precision components for microelectronics.
The machining of technical ceramics, for example, repeatedly presents manufacturers with challenges when it comes to delicate structures. Due to their high hardness and brittleness, these materials tend to form microcracks or burrs when machined using conventional methods. “The RDX1000 LWJ enables extremely precise cutting and drilling without thermal damage or mechanical abrasion,” explains Dr. Eifel.
Precise cooling channels and fine micro-holes
The aerospace industry is also increasingly using brittle-hard high-performance materials, for example for engine blades or heat protection tiles. The RDX1000 LWJ enables deeper and more precise cooling channels in heat-resistant materials without compromising their structure. “This reduces component weights and increases efficiency – a real game changer for this industry,” explains Eifel. “We are only at the beginning of a paradigm shift in the laser material processing of ceramic components,” Dr. Eifel is convinced. “By working with Synova and using it in the Schunk Group’s MACHLab, we are consistently driving forward the industrial application of laser waterjet technology.”
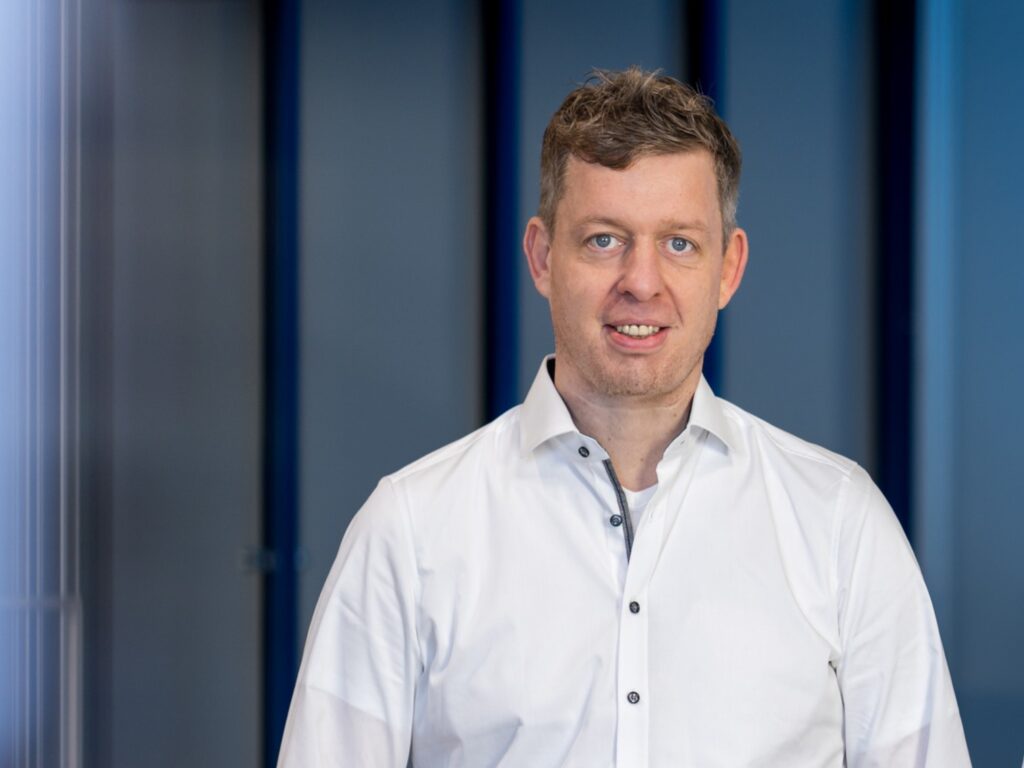

Pulsar Photonics
Pulsar Photonics GmbH is an innovative high-tech company in the field of laser technology. The company’s range of services includes laser process technology, machine manufacturing with software development and the laser systems technology division.
Since its foundation, the company has been working intensively on scaling approaches for production. For customers, the company offers exclusive services ranging from professional application development and ramp-up to the construction of automated production machines with service and know-how transfer. Pulsar Photonics is continuously investing in its own production capacities for single part and series production with (ultra) short pulse lasers. The core processes are structuring, drilling and precision cutting.
Pulsar Photonics GmbH is headquartered in Aachen and operates two production plants there. The company was founded in 2013 as a spin-off of the Fraunhofer ILT in Aachen and was financed in its growth phase by the Hightech Gründerfonds HTGF, Bonn. Pulsar Photonics has been part of the Schunk Group since 2021.
With more than 100 employees today, the fast-growing and profitable company is a German SME and part of the LaserRegionAachen structural change initiative.
Synova S.A.
Synova S.A., headquartered in Duillier, Switzerland, has been a pioneer in advanced laser cutting systems for over 25 years. The integration of our innovative Laser MicroJet technology, which combines a laser in a hair-thin water jet, into a robust industrial CNC platform, offers great results for the machining of a wide range of materials. Our unique technology provides customers significant efficiency improvements, unparalleled cutting quality, and enhanced precision across various applications. Visit our website to learn more www.synova.ch.
Pictures Press Release – Download

Press Contact
Sonja Wichert
Phone: +49 (0) 2405 49 504 – 36
E-Mail: info@pulsar-photonics.de
Pulsar Photonics GmbH
Alte Würselener Str. 13, 52080 Aachen
Website: www.pulsar-photonics.de/en