Technology Laser drilling
In addition to the use of various laser beam sources, different process approaches are also available for laser drilling. These differ according to the achievable quality and the drilling time. Pulsar Photonics uses all drilling methods described below in its contract manufacturing.
Single pulse drilling
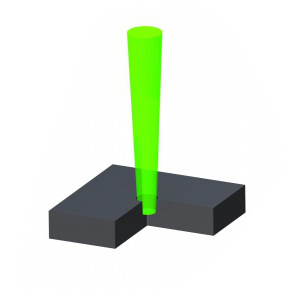
The simplest type of laser drilling is single pulse drilling. With single pulse drilling, the material is drilled through with a single, long laser pulse. The melt is mostly expelled with the support of a process gas nozzle. Thin materials (< 2mm) can be drilled with high pulse energies and longer pulse durations (ms-µs range). The drilling time in relation to the material thickness is minimal, the achievable quality is limited due to the molten material.
Percussion drilling
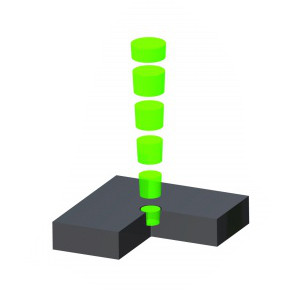
With percussion drilling, the material is successively removed by bombarding the same area with several pulses. Depending on the pulse duration of the laser used, holes up to 20 mm deep are possible. With single and percussion drilling, the laser beam is stationary during the process. The hole diameter correlates with the focus diameter on the workpiece. The drilling time is short, the qualities that can be achieved depend on the pulse duration used. The shorter the pulse duration, the higher the quality. Particularly with short pulse durations (ns-ps-fs), the entry diameter of the bore is always larger than the exit diameter.
Trepanning

With laser drilling by trepanning, the laser radiation is guided around a center point (usually the center of the borehole) during the drilling process. The diameter of the bore is widened, which is why the bore diameter can be made significantly larger than the focus diameter. The widening of the hole is generated by a cutting process.
The smoothness of the drill wall during trepanning is favored by the previous percussion process, as the melt that occurs can escape from the underside of the drill hole. When trepanning, pulses in the microsecond to femtosecond range are used and drilling depths of up to 20 mm can be achieved. When using ultra-short laser pulses, the ablation process during trepanning and percussion drilling is dominated less by a melt than by evaporation.
The lack of or reduced melt pool dynamics leads to non-vertical bore walls during laser drilling. This limits the maximum drilling depth. The drilling time is longer than with percussion drilling, and the quality is higher, especially in terms of ellipticity.
Helical drilling
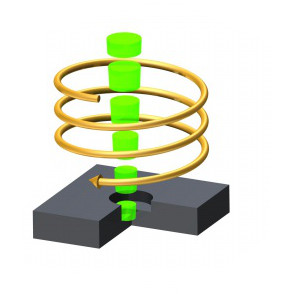
In order to overcome the problem of non-vertical bore walls and the resulting limited drilling depth, helical drilling has established itself especially when drilling with short laser pulse durations.
With helical drilling, a laser beam is guided circularly onto the workpiece via motorized helical rotating optics. Due to the circular material removal, a borehole is formed after a few revolutions of the jet. The easy adjustment of the laser beam to the drilling axis leads to a vertical drill hole even with high aspect ratios (hole diameter to drilling depth) up to 1:30.
USP helical drilling thus allows laser drilling with vertical hole walls, low ellipticity and smooth hole walls. The method allows drilling of extremely high quality, the drilling times are in the range of a few 100ms up to seconds.
Deep hole drilling (water jet guided laser drilling)

With short pulsed laser radiation, the
Waterjet method deep hole drilling with extreme
Aspect ratios (structure width / material thickness)
achieve. For this purpose, the laser radiation is in a nozzle
coaxially coupled into a thin jet of water.
The laser radiation is transmitted via this light guide
guided through the workpiece while retaining their
Focus at. This means that shaped bores and cuts with aspect ratios up to 1: 400 can be produced.