Digitalisierung in der Produktion
Vorstellung unseres Digitalen Shopfloor-Managementsystems im Sondermaschinenbau 4.0
Dr. Frank Zibner | 22. August 2024 ᛫ 15 Min.
„DiPAS“ ist eine digitale Plattform zur Produktionssteuerung, Aufgabennachverfolgung sowie der Bereitstellung von notwendigen Informationen in unterschiedlichsten Formaten. DiPAS dient zudem als Lernplattform für Azubis und anzulernende Mitarbeiter. Hierbei handelt es sich um eine eigens für die Zielanwendung des Sondermaschinenbaus entwickelte Systemlösung, welche intuitiv zu bedienen ist und rollenspezifische Funktionen zur Verfügung stellt. Die Softwarelösung ist modular und flexibel aufgebaut, sodass Sie auf abweichende Anwendungen angepasst werden kann.
DiPAS unterstützt die Transformation der Produktion im Rahmen von Industrie 4.0 und bietet ein großes Potenzial zur Effizienzsteigerung. Durch den Einsatz von KI-Algorithmen können Montageablaufpläne dynamisch angepasst werden, sodass auf fehlende Beistellungen oder unvollständige vorgelagerte Arbeitsschritte reagiert werden kann. Dies optimiert den Montageablauf effizient und zielgerichtet.
In diesem Artikel betrachten wir die Anforderungen an ein digitales Shopfloor-Managementsystem im Sondermaschinenbau, die notwendigen Funktionen und wie DiPAS diese umsetzt. Folgende thematische Schwerpunkte werden behandelt:
- Grundlegende Arbeitsfolge für die Montage einer Sondermaschine
- Möglicher Nutzen und Potential eines digitalen Shopfloor-Managementsystems
- Anforderungen an ein digitales Shopfloor-Managementsystem
- Vorteil einer Neuentwicklung gegenüber der adaptiven Nutzung einer vorhandenen Softwarelösung
- Aufbau und Funktionsweise von DiPAS
- Einsatzbereiche & Anwendungen von DiPAS
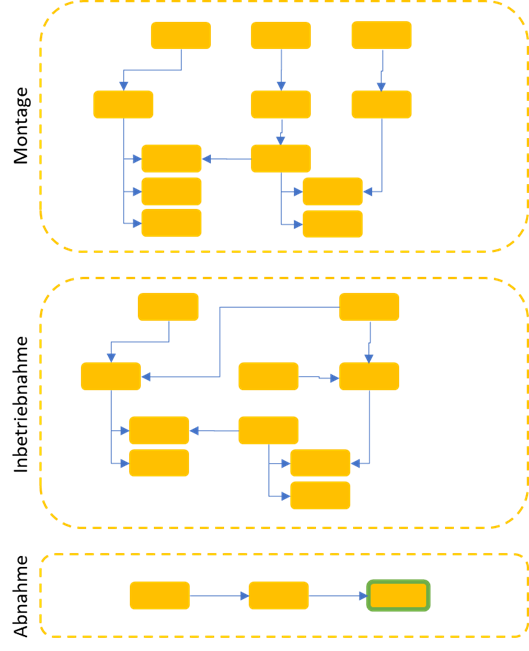
Schematischer Ablaufplan für den Aufbau einer Sondermaschine
Nach den vorgelagerten Planungsphasen eines Sondermaschinenprojektes und der Freigabe der Konstruktion sowie der E-Projektierung beginnt die Realisierungsphase durch einen Montageauftrag an den Shopfloor. Die Tätigkeiten auf dem Shopfloor sind vielseitig und beinhalten unter anderem:
- Montage & Aufstellung des Anlagengehäuses
- Einbringung & Ausrichtung des Maschinenbettes
- Montage und Verkabelung von Komponenten
- Verlegung der Medienführung
- Integration & Einrichtung der Steuerungsarchitektur
- Aufspielen & Inbetriebnehmen der Software Photonic Elements
- Inbetriebnahme & Parametrisierung der Sondermaschine
Dabei kann folgender vereinfachter Ablaufplan (siehe links Abb. 1) betrachtet werden.
Die Reihenfolge der Einzeltätigkeiten ist initial basierend auf Erfahrungswerten aufgestellt und bildet die Grundlage der Workflow-Struktur eines digitalen Shopfloor-Managementsystems. Dabei können diverse Tätigkeiten in alternativen Reihenfolgen oder parallelisiert angesetzt werden. Die hieraus resultierende Veränderung in der Effizient des Aufbaus der Sondermaschine gilt es experimentell durch den Einsatz eines solchen Shopfloor-Managementsystems zu evaluieren. Eine nachgeschaltete Auswertung und die dauerhafte Umsetzung des effizientesten Ansatzes kann langfristig Mitarbeiterkapazitäten pro Projekt einsparen.
Eine Übersicht unserer Laseranlagen finden Sie hier
Warum ein digitales Shopfloor-Managementsystem nutzen?
Die Anzahl von Einzeltätigkeiten ist den entsprechenden Mitarbeitern auf dem Shopfloor weitestgehend bekannt. Eine Reihenfolge in dessen Bearbeitung folgt oftmals einem Best-Practice Ansatz und kann von Mitarbeiter zu Mitarbeiter variieren. Teilweise ist der Produktionsleitung im Gegenteil hierzu nicht jede Einzeltätigkeit in ihrer Granularität bewusst, sodass es sinnvoll erscheint, ein gemeinsames Verständnis sowie die Abbildung der notwendigen Arbeitsschritte zu schaffen. Hier kann ein digitales Shopfloor-Managementsystem als gemeinschaftliche Plattform genutzt werden, um die Arbeitsschritte strukturiert und logisch ineinandergreifend oder aufeinanderfolgend darzustellen.
Der maximale Nutzen kann nur gemeinschaftlich erreicht werden. Dazu ist es notwendig, dass Produktionsleitung, Shopfloor-Coaches und Mitarbeiter gemeinsam das Modell aufstellen, diskutieren und optimieren. Dies gewährleistet die bestmögliche Datenlage und schafft ein Commitment für die Einführung und Nutzung des Tools.
Typische Mehrwerte eines digitalen Shopfloor-Managementsystems umfassen:
- Klare und definierte Arbeitsfolge
- Vernetzung mit dem Warenwirtschaftssystem und Aufzeigen von tatsächlich durchführbaren Tätigkeiten basierend auf vorhandenen Beistellungen und abgeschlossenen vorgelagerten Tätigkeiten
- Qualifikationsabhängiges Anzeigen von Tätigkeiten
- Digitale Bereitstellung relevanter Informationen für jede Tätigkeit – Tätigkeitsbeschreibung, Datenblätter, Montagevideos, Sicherheitsanweisungen, Auflistung von Arbeitsmitteln, uvm.
- Zugriff auf das CAD PDM System und dreidimensionale Darstellung von Baugruppen und Bauteilen inkl. Explosionsansicht
- Anlernen von Tätigkeiten für neue und ungelernte Mitarbeiter weitestgehend ohne Montagecoach
- Rückmeldung über Arbeitsfortschrift, Arbeitsfehler oder Defekten an Komponenten
- Tracking des Arbeitsflusses und Auswertung der ganzheitlichen Effizient in der Montage
- Möglichkeit der Restrukturierung der Arbeitsabfolge zur Effizienzsteigerung
- Sicherstellung der Vollständigkeit aller Arbeitsschritte im Sinne des Qualitätsmanagements
- Life Priorisierung von einzelnen Tätigkeiten
Warum das Rad neu erfinden, wenn es bereits vergleichbare Produkte gibt?
Bestehende Lösungen sind oft für spezielle Anwendungsfälle entwickelt und weisen daher viele Kompromisse auf. Während der Evaluierung haben wir bestehende Lösungen getestet und adaptiert. Diese Software stammte aus der zerspanenden Bearbeitung und wurde für Sondermaschinen angepasst. Jedoch zeigten sich während der Testphase erhebliche Mängel in der Bedienbarkeit und Darstellung, was zur Entscheidung führte, eine neue Softwarelösung zu entwickeln.
Die Akzeptanz der Software ist entscheidend für den Erfolg der Einführung. Sind die Kompromisse bei der Nutzung zu groß, ist eine Neu- oder Eigenentwicklung die logische Konsequenz. Die Qualität und Anwendbarkeit der Software bestimmen den Nutzen und spiegeln sich im ROI wider. Eine geringe initiale Investition kann durch eine Fehleinschätzung zu einem geringeren Nutzen und Nichterreichen des ROIs führen. Daher ist eine ausführliche Bewertung der vorhandenen Lösungen essenziell.
Infos zur Steuerungs- und Bediensoftware für die Lasermikrobearbeitung von Pulsar Photonics
Wie arbeitet DiPAS und welcher Nutzen kann generiert werden?
DiPAS bietet zwei Nutzeroberflächen – die Oberfläche der Produktionsleitung (Produktionsansicht) zum Anlegen von Stammdaten und erzeugen von Projekten und die Oberfläche des Bedieners (Montageansicht). Innerhalb der Produktionsansicht können Stammdaten wie Nutzer, Qualifikationsbeschreibungen, Aufgaben und Projekttypen angelegt werden. Zudem können Datenblätter und Dokumente hochgeladen werden, welche später mit Aufgaben oder Begriffen verlinkt werden können. Die notwendigen Aufgaben können in Listenform oder graphisch unterstützt (vgl. Abbildung 2) angelegt werden. Die Produktionsoberfläche ermöglicht zudem eine Visualisierung in Echtzeit des Maschinenprojektes (Synchronisierung Produktionsansicht und Montageansicht). Zudem können durch den Montageleiter einzelne Tätigkeiten priorisiert werden, welche dann auf der Montageansicht hervorgehoben als oberste Tätigkeit erscheinen. Somit besteht die Möglichkeit der Echtzeitsteuerung und damit das dynamische Reagieren auf ungeplante Vorkommnisse.
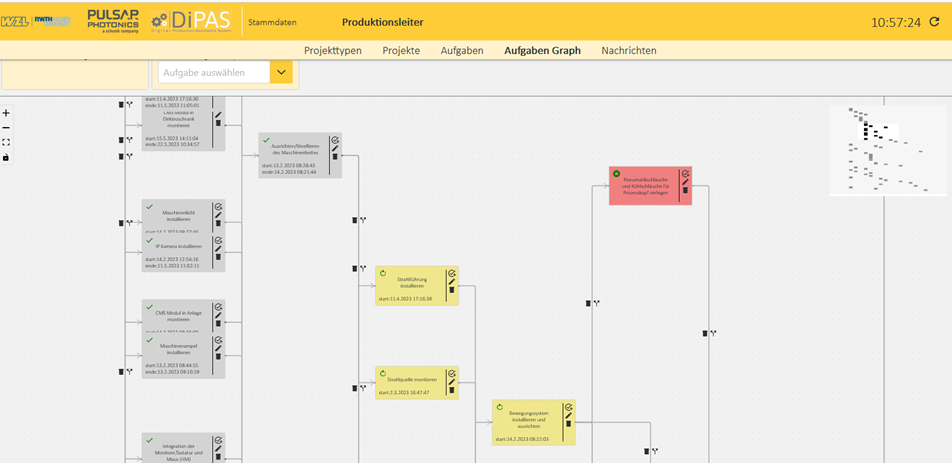
Der Mitarbeiter nutzt die Montageansicht. Dort werden Tätigkeiten basierend auf Verfügbarkeit und vorlaufenden Tätigkeiten angezeigt und bearbeitet. Der Mitarbeiter meldet sich per NFC-Autorisierung an und erhält qualifikationsrelevante Aufgaben. Mit dem Öffnen der Tätigkeit wird die Durchlaufzeit gestartet und der Mitarbeiter wechselt in die Hauptansicht der Tätigkeiten (vgl. Abbildung 3). Folgende Informationen und Optionen werden visualisiert:
- Bilddarstellung des komplettierten Zustandes
- Benötigte Werkzeuge
- Benötigte Materialien
- Benötigte Qualifikationen
- Arbeitssicherheitsrelevante Hinweise sowie allgemeine Hinweise zu der Tätigkeit
- Interaktive Montagebeschreibung mit Bebilderung und schrittweiser Anleitung
- Verlinkung zum PDM System für eine interaktive 3D Betrachtung (vgl. Abbildung 4)
- Montagevideo
- Möglichkeit zur Rückmeldung an den Montageleiter (Beschädigungen, Rückfragen, fehlendes Material, …)
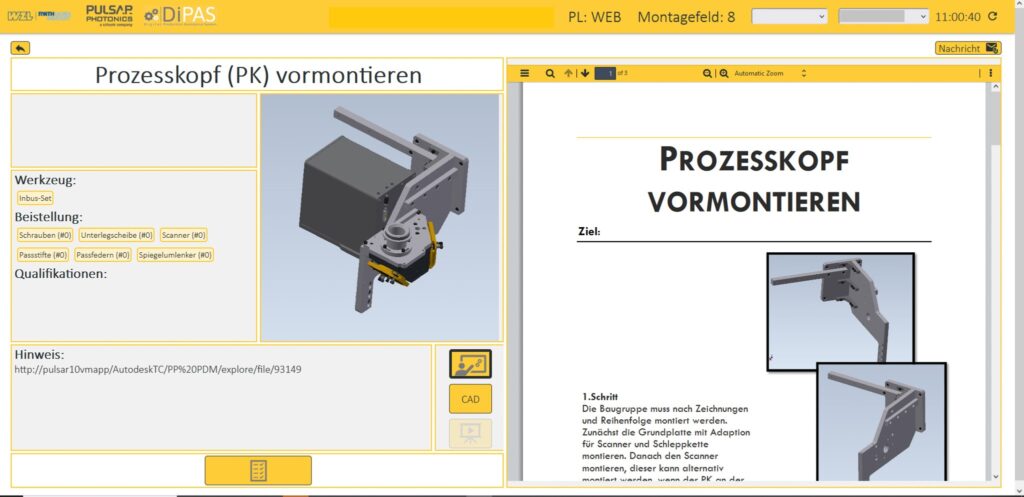
Abbildung 3: Bedieneroberfläche mit angezeigter Montageanleitung (rechts). © Pulsar Photonics GmbH.
Der rechte Bereich der Oberfläche ist dabei als dynamisches Fenster ausgelegt, welches wahlweise die Montageanleitung, das PDM System oder das Montagevideo anzeigt. Innerhalb dieses Fensters kann in allen drei Varianten gezoomt werden. Dabei erfolgt die Steuerung der Vergrößerung intuitiv per Touch-Bewegung anlog zu den etablierten Smartphone-Vorgängen. Die Bedienung der Montageoberfläche erfolgt ausnahmslos per Fingerberührung, sodass ein effizienter Ablauf gewährleistet ist.
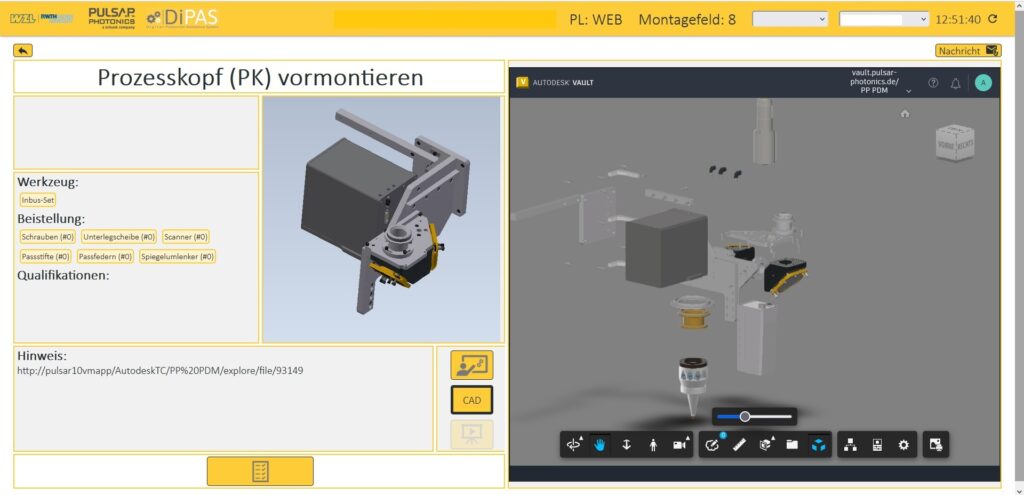
Ist die Tätigkeit abgeschlossen, kann der Mitarbeiter diese über das ‚Document of Completion‘ abschließen. Relevante Einzelvorgänge werden als Checkliste abgefragt, und ein Abschluss ist erst bei vollständiger Bestätigung möglich. Dies erhöht die Qualität der Fertigung und unterstützt die Mitarbeiter.
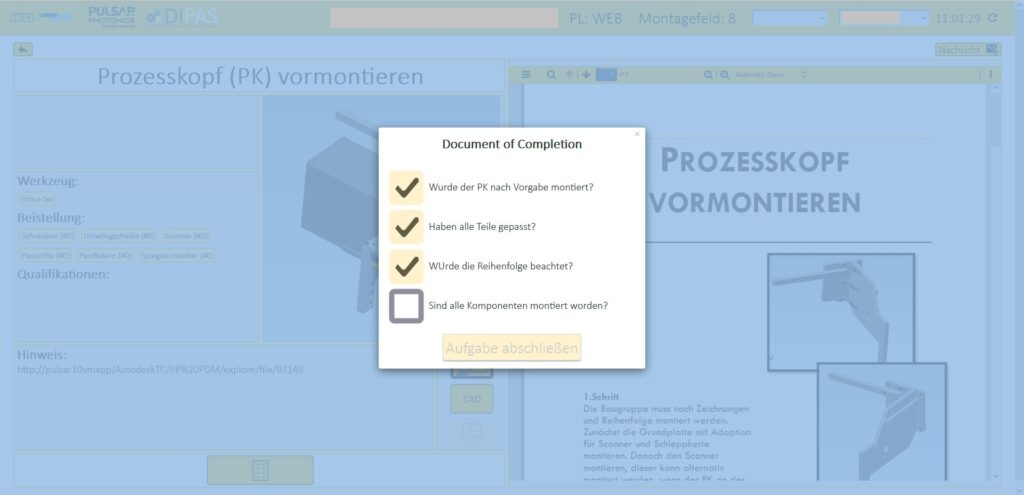
Folgender Mehrwert kann durch die konsequente Benutzung eines digitalen Produktionsassistenzsystems wie DiPAS geschaffen werden:
- Erhöhung des Verständnisses von Arbeitsabläufen
- Hinterfragen und Restrukturieren von Arbeitsfolgen für einen optimierten Arbeitsfluss
- Zentralisierte Bündelung der Bereitstellung von Informationen
- Etablierung eines Standards innerhalb der Montage (Qualitätserhöhung)
- Sicherstellung der Vollständigkeit innerhalb der Montage
- Anlernen von Personal durch umfängliche Montageanleitungen und Montagevideos (teilweise) ohne Direktbetreuung
- Erfassung von Durchlaufzeiten für Tätigkeiten sowie Analyse der Effizienz von genutzten Modellen
- Echtzeit Rückmeldung von Störungen im Montageablauf
- Zusammenführen aller relevanten Abnahmeschritte und Checklisten in einer Plattform
- Realisierung von Effizienzsteigerungen durch kontinuierlichen Verbesserungsprozess (KVP)
- Darstellung von Abnahmelisten und Testroutinen
Einsatzbereiche
Die intuitive Bedienung sowie das übersichtliche Zusammenführen aller Informationen und der Zugriff auf die 3D Datenbank sind Herausstellungsmerkmale für den Erfolg von DiPAS. Die Mitarbeiter arbeiten gerne mit DiPAS und kommunizieren proaktiv Änderungswünsche und zeigen damit Verbesserungspotentiale auf.
DiPAS ist modular und anpassbar. Änderungen an der Benutzeroberfläche und Anpassungen der Farbgebung sind möglich. DiPAS kann für jeden Anwendungsfall genutzt werden, der auf sequentiellen Tätigkeitsschritten basiert. Es eignet sich für komplexe Produkte wie Sondermaschinen und für die Montage kleinerer Baugruppen. Auch für die Erstellung digitaler Produkte oder Testroutinen kann DiPAS eingesetzt werden.
Gerne beraten wir Sie hinsichtlich unseres digitalen Produktionssystems und beantworten Ihre Fragen
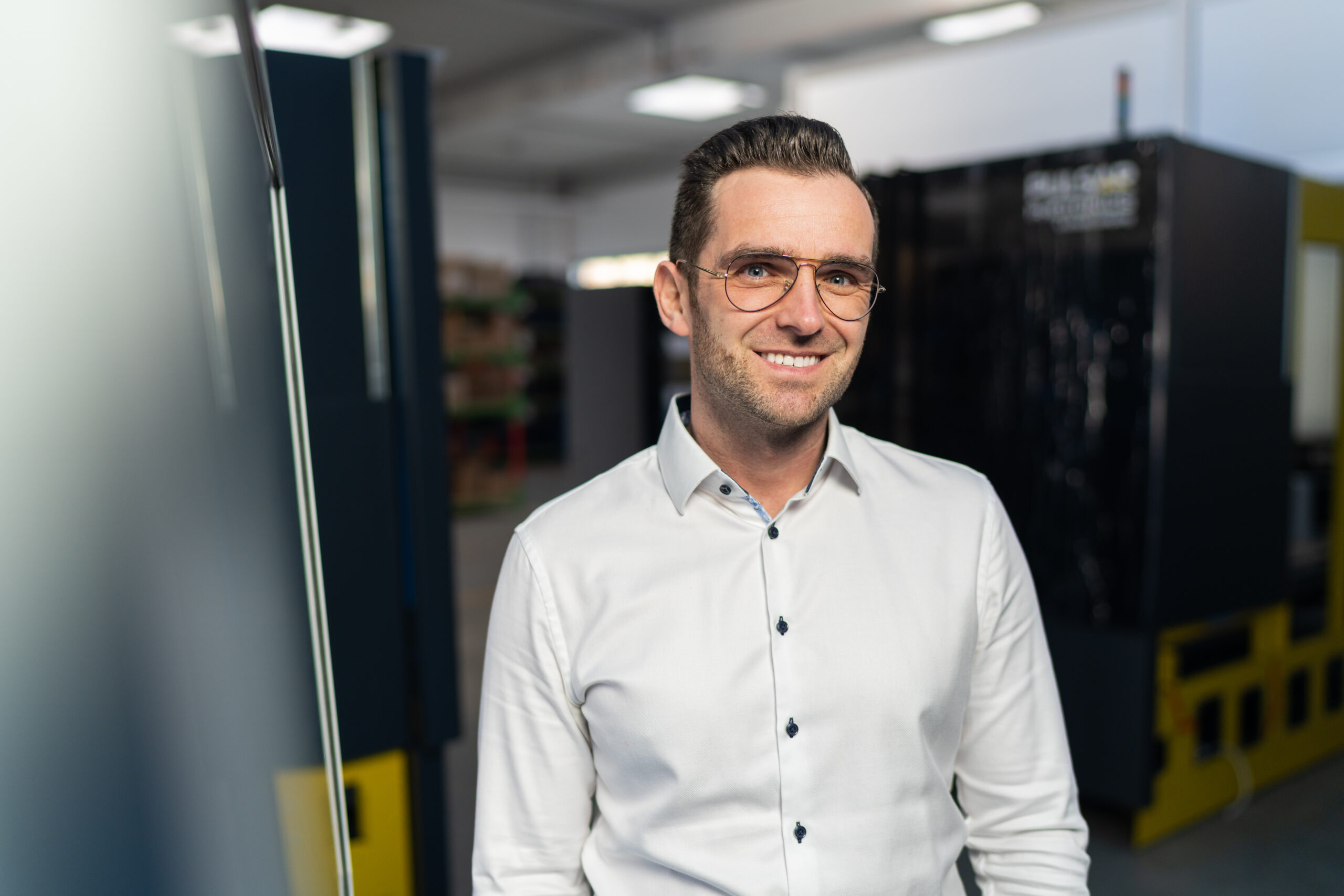
Mehr über den Autor:
Dr. Frank Zibner
Dr. Frank Zibner ist Leiter des Geschäftsbereiches Anlagenbau bei Pulsar Photonics.
Nach dem Maschinenbaustudium an der RWTH mit der Vertiefungsrichtung Luftfahrtechnik promovierte er am Fraunhofer Institut für Lasertechnik ILT im Bereich der Lasermikrobohrverfahren. Im Rahmen der Verantwortlichkeit für den Geschäftsbereich Anlagenbau werden die Tätigkeitsschwerpunkte Projektmanagement, Design & Konstruktion, Montage sowie Inbetriebnahme und Automatisierung adressiert.